Digitalisation – more than a Mayfly!
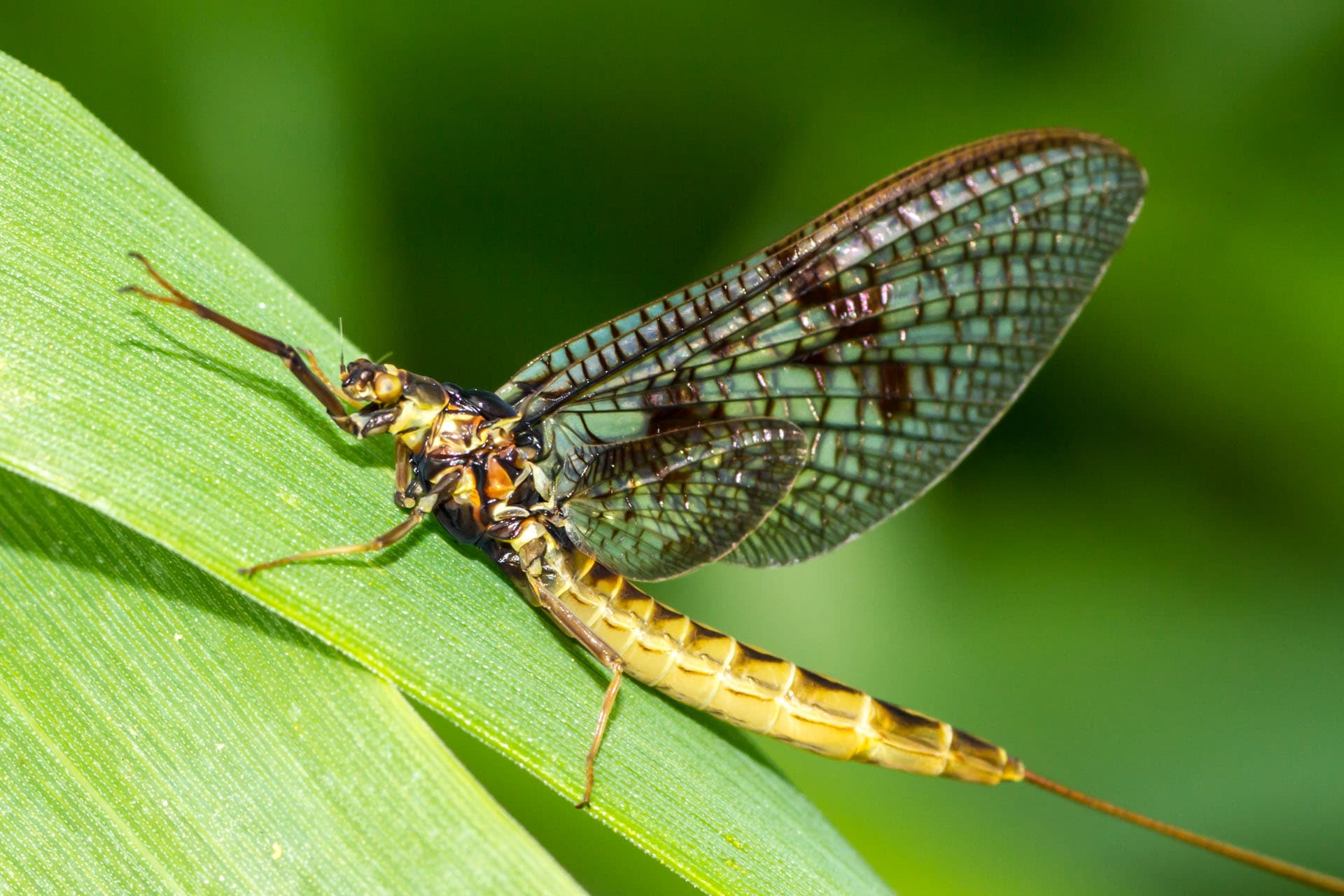
When we consider that we are now talking about Industry 4.0 it begs the question of what will come next? What will Industry 5.0 bring? Will digitalisation still be on the agenda when we are living in the age of that new buzz-word? And thinking about telecommunications and your smart-phone, are you ready for the inevitable obsolescence of G3 and G4 with the imminent introduction of G5? Perhaps the use of numbers in this context speaks of a continuous evolution which reflects a primary force that has driven mankind and the natural world to the wonders that exist today.
Coming to the natural world, in many countries there is a type of fly which is born and dies in the same day, it goes by different names and the biology changes around the world, but this type of insect is well known. In England it is called the ‘Mayfly’, in Germany, the ‘Eintagsfliege’. Is digitalisation also a Mayfly, a one-day-wonder? Or is it a progressive evolution of the way that we exploit and interact with digitally enabled technology to create a better world?
That idea of a progressive evolution might be a constructive and realistic way to think about digitalisation, and it means that ‘the project’ is never finished. Digitalisation has, in many respects, established its self as a long-term evolutionary process in industry. The changes that have taken place in the past, such as the implementation of sophisticated process control and ERP systems have enabled some of the latest generation of digital changes such as the use of machine learning and artificial intelligence to analyse the masses of data that has been captured over recent years.
Digital technology has been around for a long time. But the cut-off points for cost effective Application of digital are moving. Put another way, the costs of digital technology such as sensors, tracking systems, smart-phones, ultra-fast computers, mass data storage and retrieval systems, advanced wireless communications have fallen so rapidly in the past decades that the cost-benefit ratio to justify their wider Application in industry simply makes more sense now than in the past. And as the innovations continue and prices fall further, we can expect this evolution to progress further.
To explore the multiple ways that digitalisation is changing the way companies can deepen the relationships that they have with their clients; protect the safety of the general public and their employees or make it easier to do business with them, we can examine three case studies from the industrial gases sector. The cylinder gases segment of the sector is primarily a chemicals distribution business where the challenges of vehicle logistics, asset management and interaction with a diverse customer base are bread and butter topics.
Digitalisation can deepen customer relationships
One industrial gases company has been rolling out a cylinder asset management APP which is using digitalisation to improve hospital patient outcomes. It is giving nurses more time to add the unique value that the personal-touch can bring by doing what they do best: caring, touching and feeling for the patients in their care. On the face of it, the APP could be a cylinder asset management tool – clearly in the sweet spot of process improvement. But when we scratch beneath that we can see that the APP is enabling so much more.
From a technical functionality perspective, we can describe the APP as using 2D barcode scanners to track the location of medical oxygen gas cylinders as they are delivered to hospitals and as they move around inside hospitals from the stores to wards. The tangible benefits to the industrial gases cylinder distributor can be identified as reduction of the overall cost to serve and improving the utilisation of the cylinders, which are valuable capital assets thereby improving return on capital employed. The ground-breaking point is that the APP is also used by hospital staff. This means that they can see exactly where their cylinder inventory is. Gone are the days when the ward sisters needed to play on the safe side and always order a few extra cylinders to store away in a secret cupboard for that awkward emergency event when no full cylinders could be found.
With full visibility of the cylinders around the hospital, staff are reassured that there will be adequate cylinders to fulfil the needs of their patients. Furthermore, when that emergency strikes, identification of the location of the closest cylinders is possible with just a few finger-clicks. It saves the hospital time and money. But, more importantly it means that the nursing staff are free to concentrate on their patients. Hospitals using the App have moved their conversation with their industrial gases supplier beyond transactional elements into discussions related to a partnership to deliver better patient care.
The concept that the APP employs can be extended to add value and improve patient outcomes beyond medical oxygen cylinder tracking. Beds are another expensive capital item that hospitals need to track and manage. Using the APP for tracking additional assets means even more added-value to the hospital. The digital transformation is thereby enabling a transformation of the relationship between the medical gases supplier and the hospital into one which will have the depth to stand the test of time.
Industry 4.0 means ease-of-doing-business
Electronic Data Interchange, or EDI, has been used for many years to improve the process of billing between industrial gases suppliers and their customers. It is still an ideal solution for many larger and mid-sized cylinder gases users. But, for smaller customers who are always on the move like refrigeration contractors or welding repair specialists who are never in the office but always at their place of work something extra is required. The same goes for gas users in the very largest of customers who may be working in remote corners of vast refineries, mining complexes or working on gas pipelines that straddle thousands of kilometres of land.
With this customer segment in mind, some industrial gases cylinder distributors have developed Mobile Phone based solutions. They allow cylinder gas users to scan cylinder bar-codes using their smart-phone for the purposes of inventory management such as stock taking and re-ordering product on-line. Gone are the days of ambiguous and frustrating conversations with the order-taking team that go something like this: “Hi, it’s Fred here from the Big Mine Company. I’ve forgotten my account number, but I need another 6 cylinders of oxygen. I think that they are called G size. Or no, wait are they E size? And the purity is about 99%, oh, sorry it’s probably 99.5% that we want. I need them delivered to the stores on highway 6, not the normal stores at gate 2, but I’ve forgotten the drop point code you use for that”.
With so many possibilities to order the wrong product in the wrong cylinder size to be delivered to the wrong location and invoiced to the wrong department the idea of one-click re-ordering using the Mobile Phone barcode reader is a real time saver that helps everybody to get it right first time, making it easier to do business.
Clearly, the mobile phone needs to be substituted for an intrinsically safe device for this kind of idea to work on refineries and other hydrocarbon processing operations… but the pace of evolution on the hardware side of digital technology has solved that problem also.
Is your organisation contemplating the next phase in the progressive digitalisation of your business operation to improve bottom line results? Nexant stands ready to offer our independent advice to clients in the chemicals production, chemicals distribution and energy sectors who are wanting to explore their next steps in the digital evolution. Contact the author, Stephen B. Harrison – Principal, Germany at Nexant for further information.
The Author